- PRODUCTS
-
-
-
Latitude Edge Class 2 SRL-Ps
Combine best in class engineering with Class 2 versatility for use on a wide range of job sites, including the most extreme leading-edge environments.
-
- KNOWLEDGE
- COMPANY
- NEWS
- BLOG
Check Out Our News Topics
Q2 2025 Spotlight
What Does “Safety Up” Mean for You? As we grow, safety is elevated for everyone!…
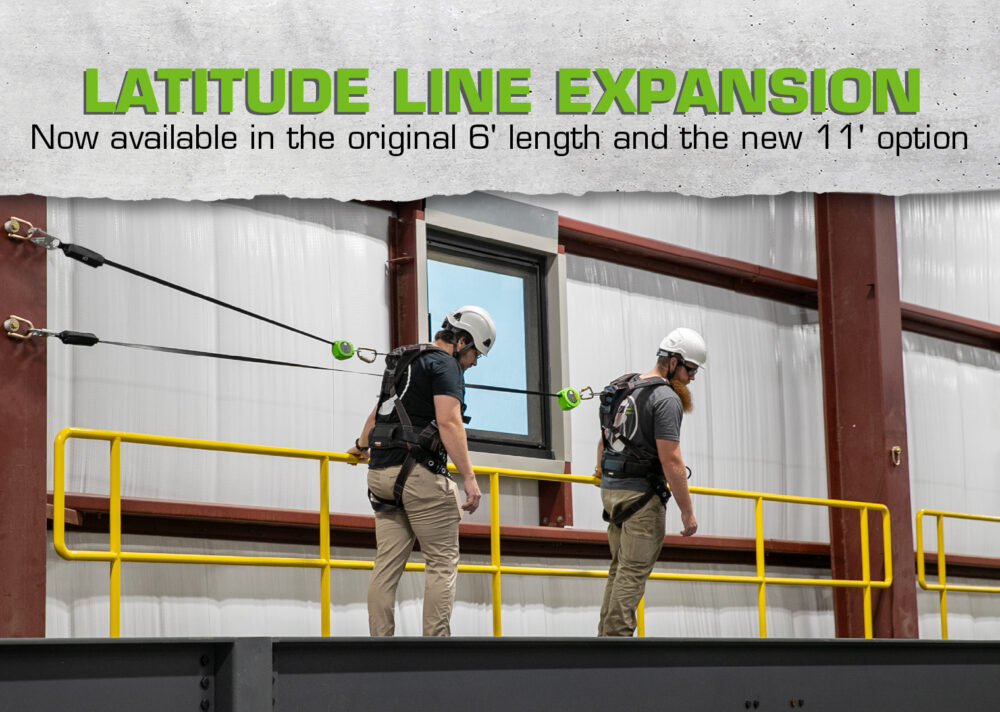
Latitude Line Extension
Get almost TWICE the reach without the bulk with the new addition to the Latitude…
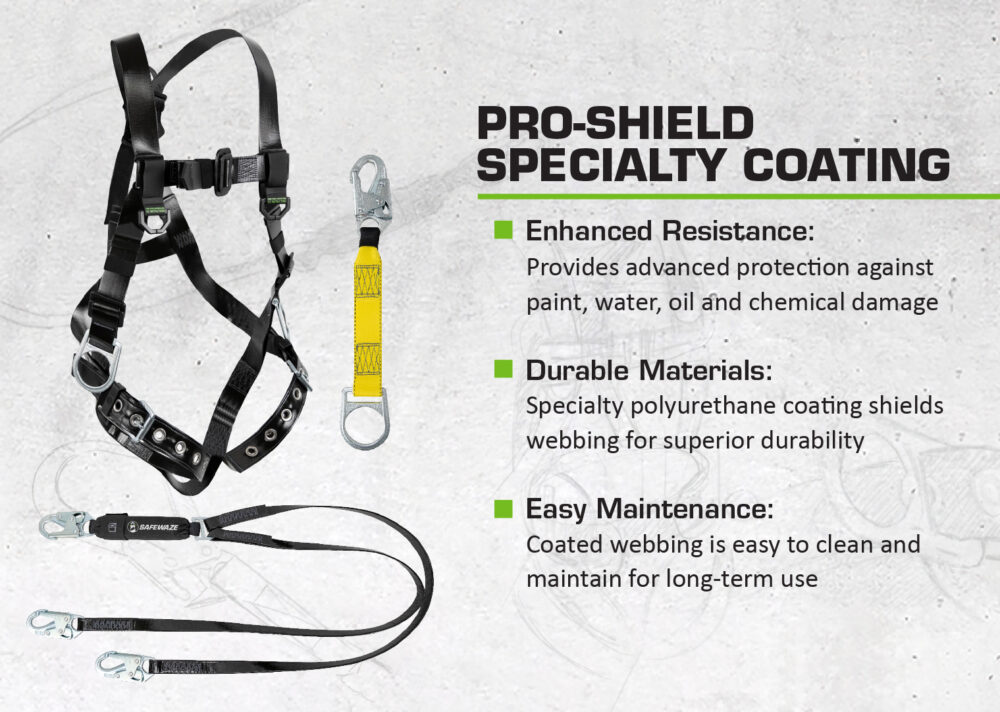
PRO-Shield Specialty Coated Line
Tough jobs meet their match with the new PRO-Shield Speciality Coated Line! Engineered with a…
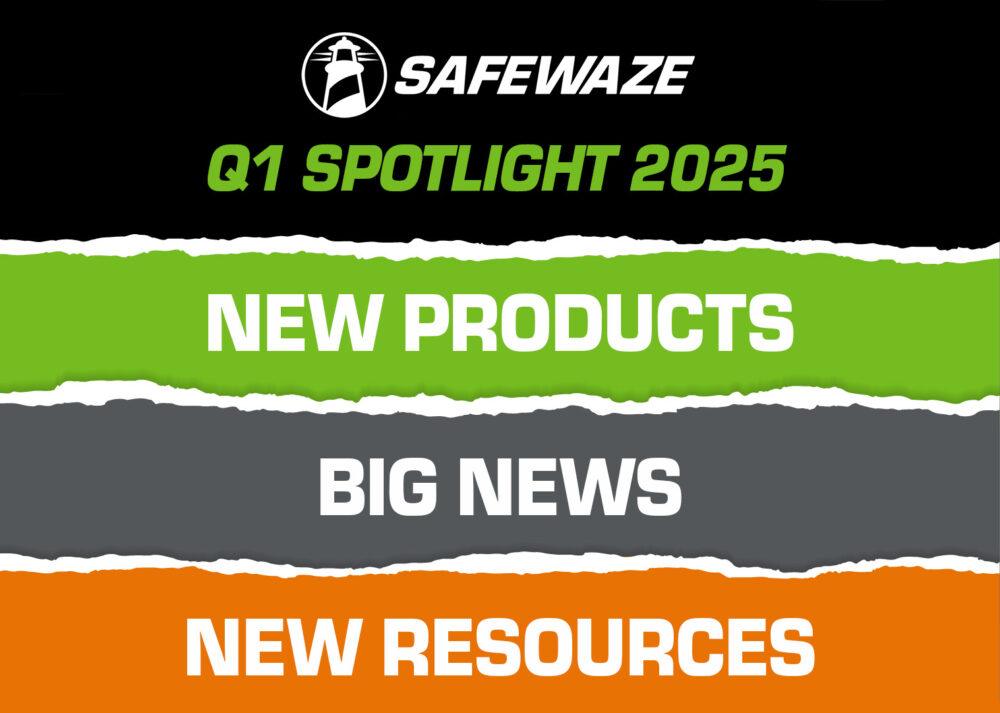
Q1 2025 Spotlight
Reading this spotlight will make you smarter. Guaranteed — learn something or your money back!…